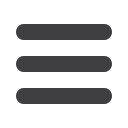
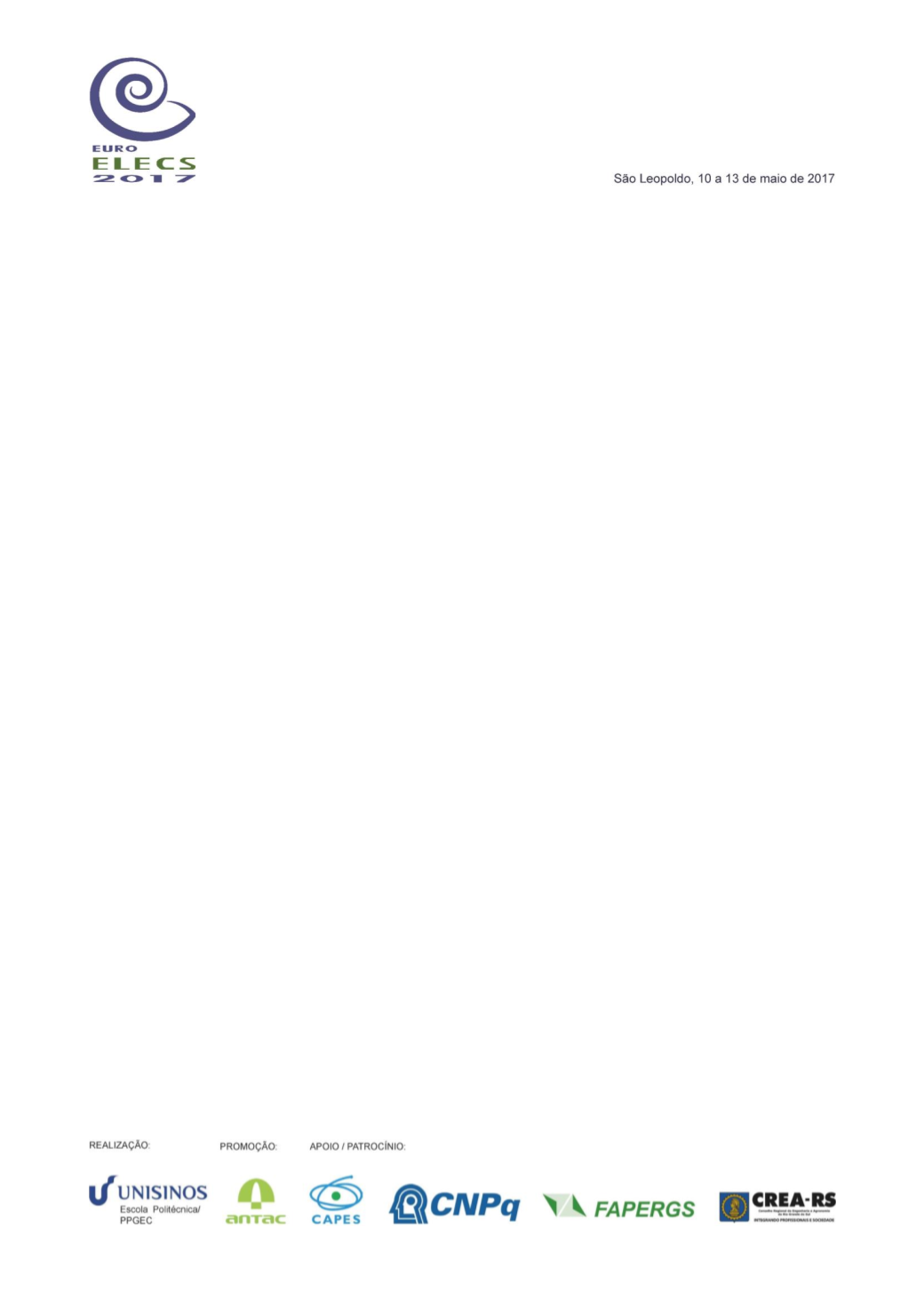
969
material, em reagir com o hidróxido de cálcio proveniente da hidratação do cimento para formar
silicato de cálcio hidratado adicional. Cordeiro e Désir (2010) ao analisarem diversos teores de
substituição de cimento Portland por RCV, verificaram que a introdução de material cerâmico
contribuiu para o aumento da resistência dos concretos analisados.
No que se refere à utilização do RCV para a produção do LC
3,
Scrivener (2014) explica que, a argila
é único material com potencial para contribuir significativamente na redução do clínquer (e emissões
de CO
2
), pois torna-se reativa quando calcinada a temperaturas entre 600ºC e 800ºC. O LC
3
é um
cimento com baixa concentração de carbono e é composto por uma mistura ternária de argila
calcinada, calcário e clínquer. Ainda segundo Scrivener (2014), o LC3 apresenta duas grandes
vantagens para produção sustentável, uma delas, é que cerca de 45% da mistura é composta por
resíduos, e a segunda, é que o teor de clínquer é reduzido em cerca de 50%. A autora verificou,
através da análise do ciclo de vida, que o LC3 pode reduzir em até 30% as emissões de CO
2
, e
economizar até 50% de calcário, se comparado ao cimento convencional. Além das vantagens
apresentadas, o LC
3
apresenta durabilidade e resistência comparáveis aos cimentos convencionais.
Neste contexto, tendo em vista a viabilidade de utilização do RCV para a produção de LC
3
, bem
como, a sua utilização em substituição parcial ao cimento Portland, este trabalho foi proposto. Para
isso, levou-se em consideração, as características químicas, físicas e mineralógicas de um RCV e
de um RCV Produzido em Laboratório (RCVPL) à diferentes temperaturas, e, principalmente, a
capacidade pozolânica destes materiais. Espera-se que estudos deste tipo possam contribuir para
pode melhorar a sustentabilidade do cimento Portland, que é o aglomerante mais empregado na
construção civil
2. MATERIAIS
2.1 CERÂMICA VERMELHA
2.1.1 RESÍDUO DE CERÂMICA VERMELHA (RCV)
O RCV utilizado teve origem a partir de blocos cerâmicos coletados de um mesmo lote de produção,
que segundo informações do fabricante, teve temperatura média de queima estimada entre 700°C
e 750°C. O beneficiamento do RCV na forma de pó, foi realizado em três etapas de cominuição,
incluindo britagem e moagem. Inicialmente, o resíduo foi submetido a um britador de mandíbulas,
após, os fragmentos de cerâmica passaram pelo primeiro processo de moagem em um moinho de
rolos, com distância entre rolos de 3 mm. Depois disso, a cerâmica vermelha foi processada mais
refinadamente com o auxílio de um moinho de bolas, onde a cerâmica permaneceu por um período
de 60 minutos. Foram utilizados 5 kg de bolas de porcelana e foram beneficiados 3kg de cerâmica,
por moagem.
2.1.2 RESÍDUO DE CERÂMICA VERMELHA PROCESSADO EM LABORATÓRIO (RCVPL)
A origem do RCVPL é a mesma do RCV, porém, a coleta do material foi realizada antes da
calcinação na indústria, com o intuito de fazer a queima destes blocos cerâmicos crus com controle
específico de temperatura em laboratório. Os blocos foram calcinados em um Forno Mufla marca
Sanchis e modelo DTT 1.250, com um patamar de aumento de temperatura de 150°C/h até a
queima estável por 8 horas nas temperaturas de 650°C, 750°C, 850°C e 950°C. O beneficiamento
do RCVPL na forma de pó foi realizado em três etapas de cominuição, mesmo processo realizado
com o RCV, tendo com diferenciação a etapa de moagem. Após o resíduo ser submetido ao britador
de mandíbulas, os fragmentos dos blocos foram moídos diretamente em moinho de bolas sem
excentricidade, mesmo equipamento empregado na última etapa do beneficiamento do RCV. Ainda,
depois disso, o material com dimensão de grão menor que 0,3 mm foi submetido a moagem refinada
em um moinho de bolas excêntrico (Periquito).