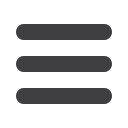
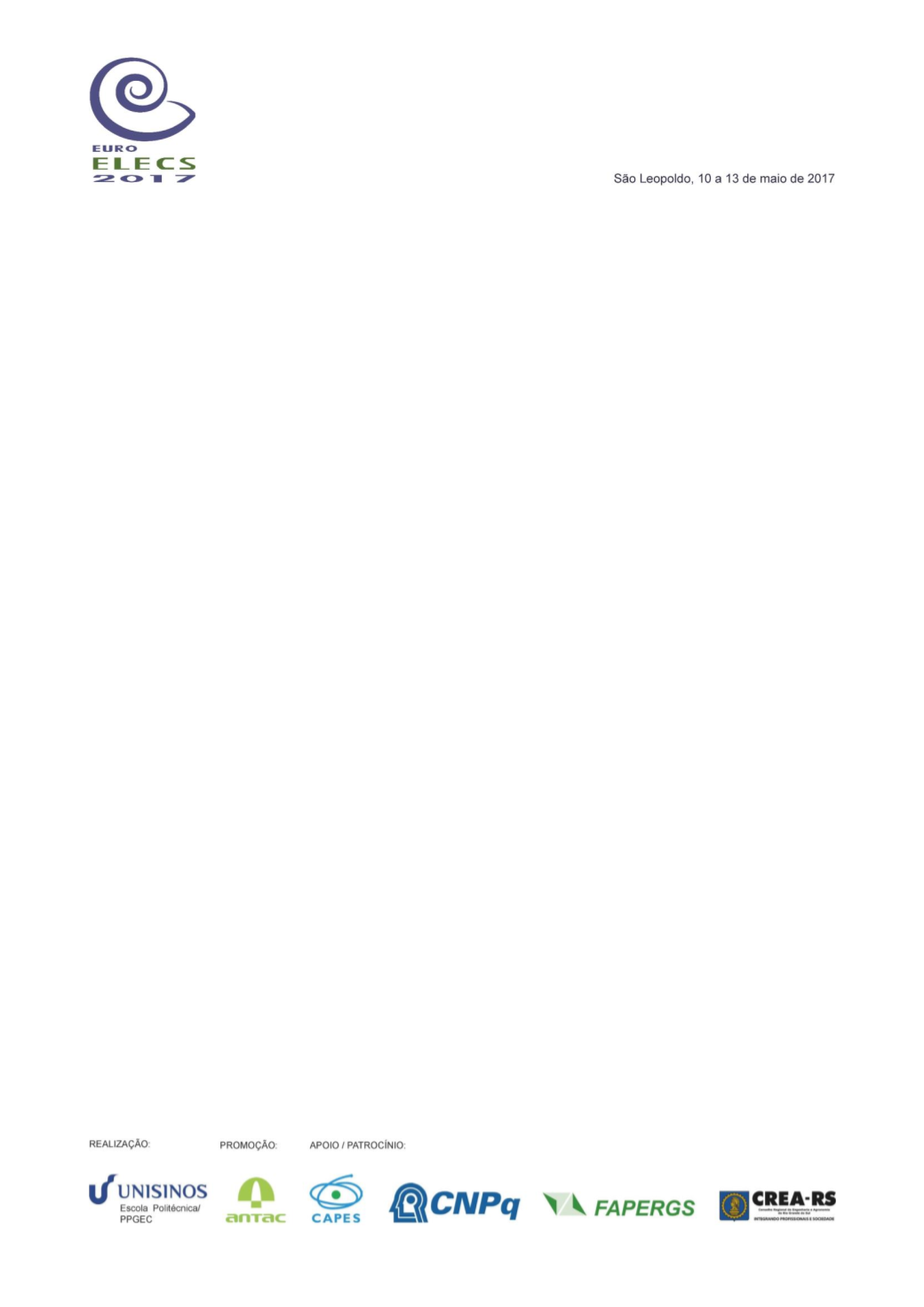
1440
test. Three proportions were used: intermediate ratio (1: 3.0), rich ratio (1: 1.5) and poor ratio (1:
4.5), all expressed in a cement: dry sand mass ratio. The following substitution levels were adopted
of the fine aggregate by agate rolling powder: 0%, 15%, 30% and 45% by volume. The results
showed that the replacement of the limestone fine aggregate with agate residue was beneficial,
increasing the compressive strength and the tensile strength in the diametral compression and
reducing the capillarity water absorption. The increase in strength and water absorption reduction in
mortars with the use of the agate residue is probably due to the physical effect, which may have
provided a pore buffer serving as an adjunct to granulometry.
Keywords:
Agate; Mortar; White Portland cement; Mechanical properties; Durability
1. INTRODUÇÃO
O Brasil é uma das nove regiões geográficas do mundo com excepcional volume na produção de
gemas e está classificado como o maior produtor de ágata do tipo Umbu e de outras gemas. Dentro
do Brasil o estado do Rio Grande do Sul não se destaca pela variedade, mas sim pela quantidade
que produz, ocupando o terceiro lugar no país, após Minas Gerais e Bahia (BRANCO; VIEIRO,
2004).
O processo produtivo de pedras preciosas, como a ágata, gera resíduos que demandam um
direcionamento, visto que atualmente são depositados nos pátios das empresas, ocupando grandes
áreas, impermeabilizando o solo e podendo causar impactos ao meio ambiente. O ideal seria reduzir
a quantidade de resíduos em todas as fases do processo de beneficiamento (desde a extração até
o produto final). Entretanto, resíduos sempre serão gerados na maioria dos processos de
beneficiamento de materiais. (BETAT, 2006)
A construção civil apresenta-se como uma excelente alternativa para receber estes resíduos,
contribuindo para a minimização dos impactos ambientais, já que a extração de matérias-primas
utilizadas por este segmento gera grandes impactos. A coloração clara do resíduo de ágata permite
o emprego com cimento branco, visto que pode ser usada como substituição aos agregados de
calcário utilizados, geralmente, na produção de concretos e argamassas produzidas com cimento
branco.
Concretos brancos são produzidos com agregados miúdos e graúdos de cores claras, para que as
colorações não influenciam esteticamente. Para tal é adotado o cimento Portland branco, que
apresenta esta coloração por não ter em sua composição óxidos de ferro e manganês, responsáveis
pela cor cinza do cimento Portland convencional. Passuelo (2004) afirma que a simples utilização
de cimento branco não necessariamente irá satisfazer as exigências de cor, pois a cromaticidade
da mistura da matriz cimentícia depende de todos os materiais envolvidos no processo. Segundo
Kirchheim et al. (2011) inúmeros materiais inertes podem ser usados como agregados para
produção de concretos de cimento Portland branco, incluindo os calcários e as areias silicosas ou
argilosas, basaltos, mármores e granitos. Passuelo (2004) destaca que, mesmo com os agregados
graúdos apresentando parâmetros cromáticos escuros, como agregados de origem basáltica por
exemplo, os concretos manterão uma coloração clara. Desta maneira como o agregado graúdo não
fica visível na superfície do concreto, pode-se considerar que ele tem um papel menos importante,
assim apresentando pouca influência sobre a cor (FONSECA; NUNES,1998). Entretanto, o mesmo
não é válido para o agregado miúdo, pois estes têm grande influência na cor da mistura.